8 Simple Techniques For Alcast Company
8 Simple Techniques For Alcast Company
Blog Article
Things about Alcast Company
Table of ContentsThe 6-Second Trick For Alcast CompanyThe Single Strategy To Use For Alcast CompanyGetting The Alcast Company To WorkFacts About Alcast Company UncoveredSome Known Details About Alcast Company The Only Guide to Alcast Company
The subtle difference depends on the chemical web content. Chemical Contrast of Cast Aluminum Alloys Silicon promotes castability by minimizing the alloy's melting temperature and improving fluidity throughout casting. It plays a vital role in allowing complex molds to be filled up precisely. Additionally, silicon contributes to the alloy's toughness and wear resistance, making it beneficial in applications where durability is critical, such as vehicle components and engine elements.It likewise improves the machinability of the alloy, making it less complicated to refine into finished products. This way, iron adds to the overall workability of aluminum alloys. Copper raises electrical conductivity, making it advantageous in electric applications. It likewise boosts deterioration resistance and contributes to the alloy's total stamina.
Manganese adds to the stamina of light weight aluminum alloys and boosts workability. Magnesium is a light-weight component that supplies strength and effect resistance to aluminum alloys.
The 3-Minute Rule for Alcast Company
Zinc enhances the castability of aluminum alloys and assists regulate the solidification process throughout spreading. It improves the alloy's toughness and solidity.
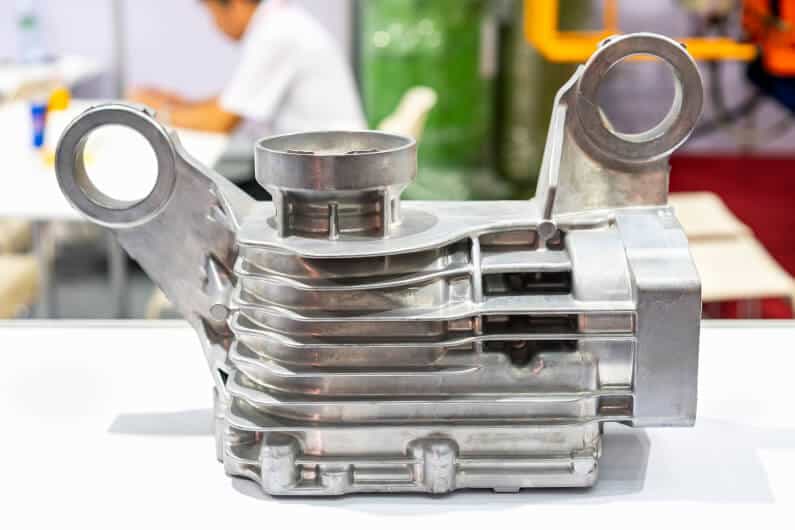
The primary thermal conductivity, tensile toughness, yield stamina, and elongation vary. Amongst the above alloys, A356 has the greatest thermal conductivity, and A380 and ADC12 have the lowest.
About Alcast Company

In accuracy spreading, 6063 is fit for applications where intricate geometries and top quality surface coatings are critical. Instances include telecommunication rooms, where the alloy's superior formability permits for smooth and aesthetically pleasing designs while keeping structural integrity. In the Lighting Solutions market, precision-cast 6063 parts produce sophisticated and reliable illumination fixtures that call for intricate forms and great thermal performance.
The A360 exhibits premium prolongation, making it ideal for facility and thin-walled components. In accuracy spreading applications, A360 is appropriate for industries such as Customer Electronic Devices, Telecommunication, and Power Tools.
Alcast Company Fundamentals Explained
Its one-of-a-kind residential properties make A360 a beneficial choice for precision spreading in these sectors, enhancing product sturdiness and top quality. Casting Foundry. Aluminum alloy 380, or A380, is a widely made use of spreading alloy with numerous unique attributes.
In precision spreading, light weight aluminum 413 shines in the Customer Electronics and Power Equipment industries. This here are the findings alloy's premium rust resistance makes it an outstanding choice for exterior applications, guaranteeing long-lasting, sturdy products in the stated markets.
Not known Factual Statements About Alcast Company
The light weight aluminum alloy you choose will significantly impact both the casting process and the properties of the final item. Since of this, you have to make your choice very carefully and take an informed method.
Figuring out the most appropriate aluminum alloy for your application will imply weighing a vast range of attributes. These relative alloy qualities follow the North American Pass Away Spreading Association's standards, and we have actually divided them into 2 groups. The first classification addresses alloy features that influence the production process. The 2nd covers attributes impacting the properties of the last item.
The Of Alcast Company
The alloy you pick for die casting directly impacts a number of facets of the casting procedure, like just how very easy the alloy is to collaborate with and if it is vulnerable to casting problems. Hot cracking, additionally called solidification cracking, is a regular die casting defect for light weight aluminum alloys that can lead to internal or surface-level rips or fractures.
Particular aluminum alloys are a lot more susceptible to hot breaking than others, and your choice needs to consider this. One more common defect found in the die casting of aluminum is die soldering, which is when the cast adheres to the die wall surfaces and makes ejection tough. It can damage both the actors and the die, so you need to look for alloys with high anti-soldering residential properties.
Rust resistance, which is already a noteworthy attribute of light weight aluminum, can differ considerably from alloy to alloy and is a crucial particular to consider relying on the ecological problems your item will certainly be exposed to (Casting Foundry). Wear resistance is another home commonly looked for in aluminum products and can distinguish some alloys
Report this page